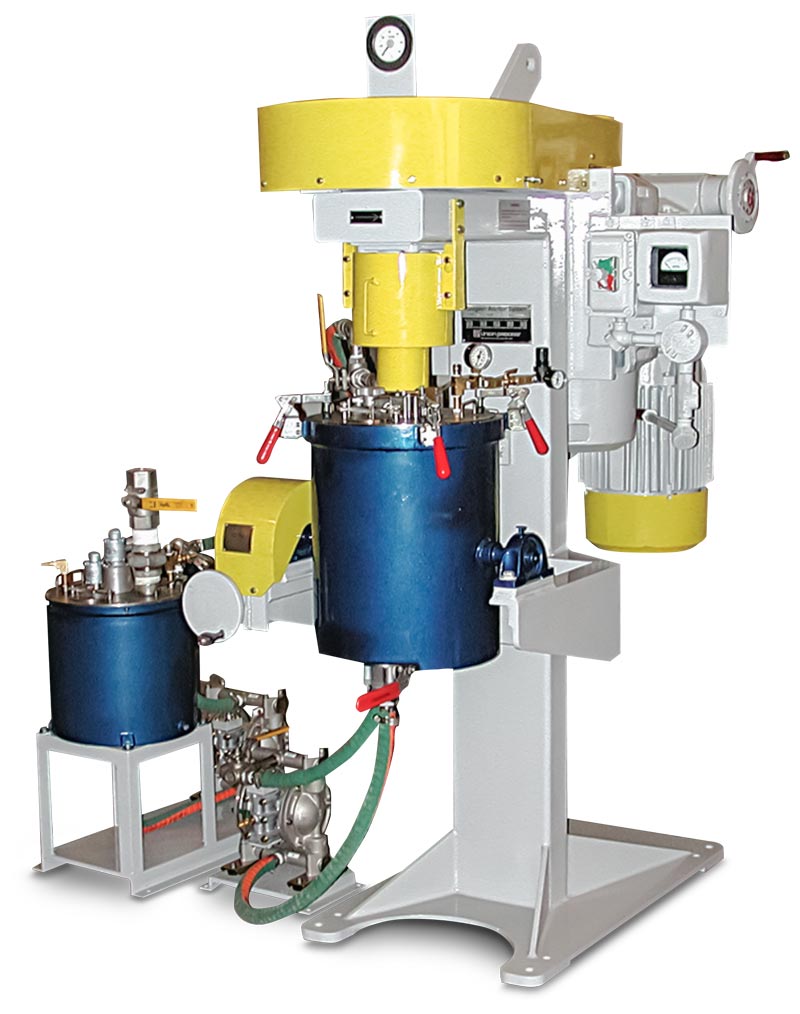
How Batch Attritors Work
The Attritor is often referred to generically as an “internally agitated high energy media (ball) mill.” Batch Attritors work ten times faster than ball mills, and are advantageous because they offer simple operation, rugged construction, and a compact design.
To learn more, visit our Education Center.
Advantages of Using a Batch Attritor:
- Ten times faster than ball mills
- Simple to operate
- Energy efficient
- No premixing required
- Minimum maintenance required
- Rugged construction
- Compact design
- No special foundation necessary
Common Applications/Industries:
- Ceramics
- Paper Coatings
- Cosmetics
- Glass frits
- Industrial Coatings
- Chocolate
- Chemicals
- Metal
- Paint
- Pharmaceuticals
- Ferrite
- Ink
- Electronics
- Catalysts
- Carbides
- Toner
- Plastic
- Rubber
- Confectionary
- Recycling
- Many Others
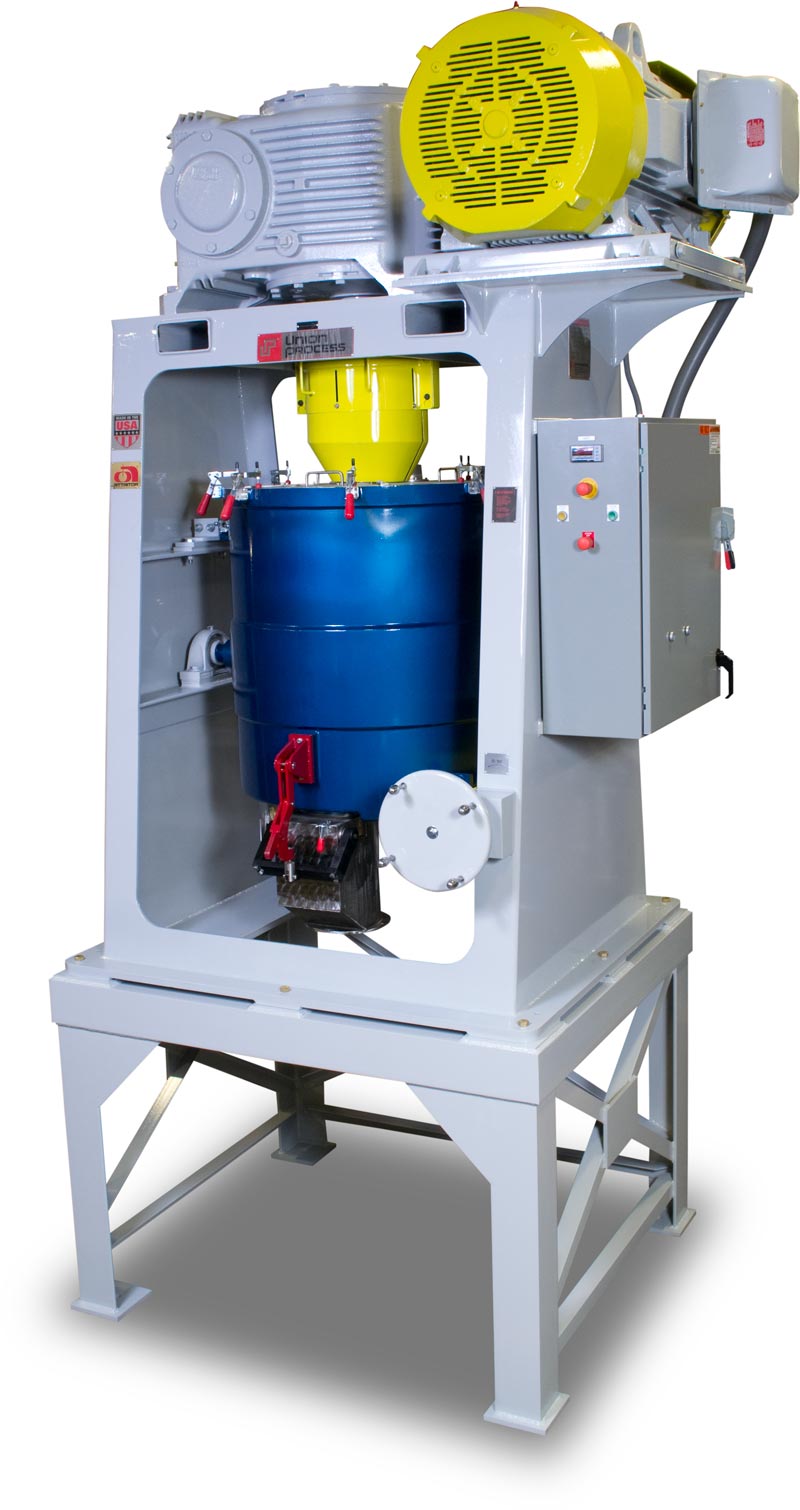
“S” Series
Batch-type Production Attritors are designated as “S” (Standard). When specially configured arms are ordered as an option the model designation becomes “SL.” When a torque meter is added to a machine, a “T” is added to the model designation. Batch Attritors range in size from a 16-gallon gross tank capacity to a 600-gallon gross tank capacity and from a 5 HP motor to a 150 HP motor. These versatile and easy-to-maintain grinding mills have been successfully used in a variety of industries to grind everything from chocolate to tungsten carbide. In addition, Attritors can be produced to meet the requirements of even the most stringent applications such as the electronic ceramic market. For this application, Attritors are available with metal-free systems to assure a contamination-free environment.
Batch Attritors offer the advantage that the material can be inspected any time during the grinding cycle. Therefore, adjustments or formulation additions can be accomplished without stopping the machine.
Attritors are ideal for long-term, heavy-duty, semi- and fully-automated production operations. They may also be used in conjunction with programmable controllers in highly sophisticated production environments.
Engineering Data
ATTRITOR MODEL | S-5 | S-10 | S-15 | S-30 | S-50 | S-100* | S-200 | S-250 | S-400 |
Gross Tank Volume (gals) | 9 | 17 | 25 | 53 | 82 | 157 | 313 | 375 | 602 |
Slurry Capacity (gals) | 4-5 | 7-9 | 10-12 | 23-25 | 34-37 | 70-75 | 140-150 | 177-187 | 280-300 |
Media Volume (gals) | 5 | 9 | 12 | 25 | 37 | 75 | 150 | 187 | 300 |
HP*** | 3-5** | 5-7.5 | 5-10 | 10-20 | 15-25 | 20-40 | 40-75 | 50-100 | 75-150 |
Height**** | 79″ | 80″ | 83″ | 89″ | 97″ | 106″ | 121″ | 129″ | 147″ |
Floor Space (W x D) | 34″x 63″ | 52″x42″ | 52″x42″ | 61″x43″ | 74″x50″ | 82″x56″ | 88″x72″ | 90″x76″ | 108″x80″ |
Machine Weight (lbs) w/o media | 1,500 | 1,800 | 2,200 | 3,100 | 3,500 | 6,000 | 10,700 | 12,000 | 16,000 |
**Features variable speed drive motor.
***High Starting Torque motors.
****Varies according to motor HP.
Equipment can be built to CE specifications, if required.
“SC” Series For Tungsten Carbide Applications
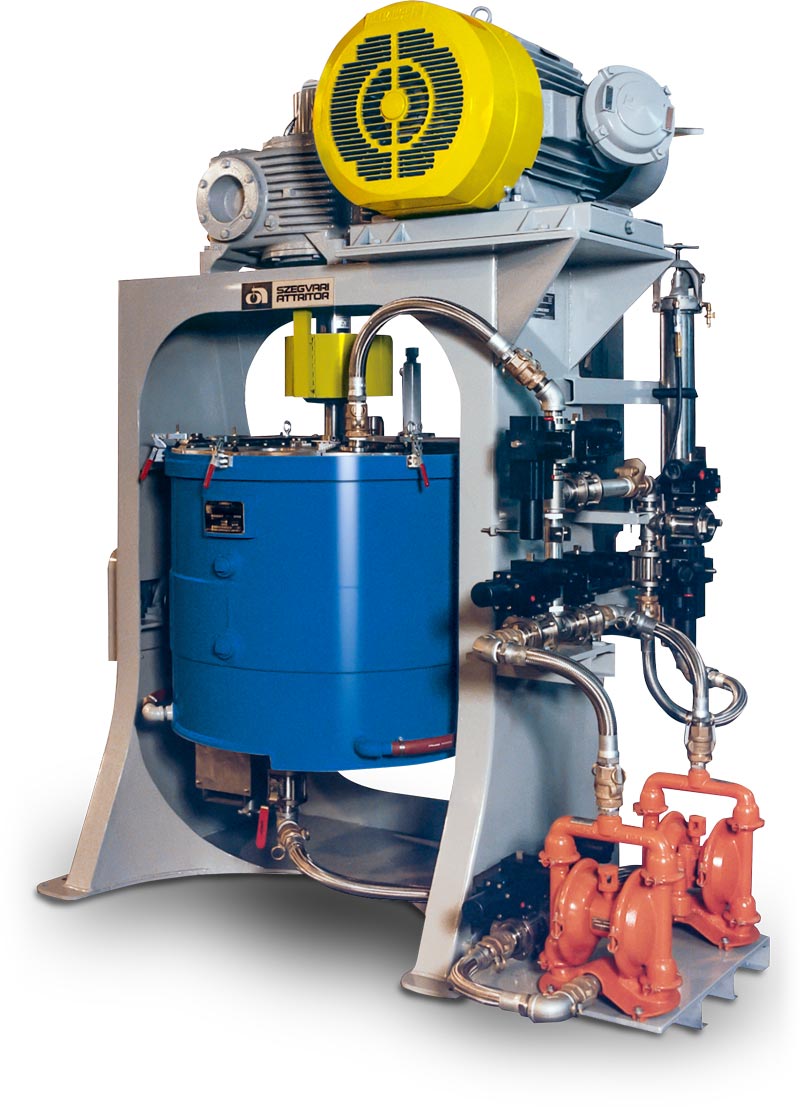
High density material such as tungsten carbide requires a specially designed heavy-duty Batch Attritor. The “SC” Series Attritor meets this special processing requirement. Available with tank capacities ranging from 7 gallons to 245 gallons and horsepowers ranging from 7.5 to 125, these powerful grinding mills feature a tapered tank to reduce load on the bottom arms for easy starting. A special lifter arm raises media and product off the bottom of the tank. Arms are sleeved with tungsten carbide to reduce wear and contamination.
The tank has a ball discharge valve and media discharge chute at the bottom for easy removal of media. A water-cooled cover with a floating teflon seal minimizes solvent loss.
The tungsten carbide Attritor is also available with an optional torque meter to precisely measure energy input for determining processing time.
A worm gear assembly attached to the tank allows the tank to be tilted. In this position, the shaft and arms can be easily removed and/or inspected and the grinding media changed, if necessary. All models come complete with a pumping system which is used to circulate material during grinding and to discharge product.
Engineering Data
ATTRITOR MODEL | SC-5 | SC-10 | SC-15 | SC-30 | SC-50 | SC-75 | SC-100 | SC-150 | SC-200 |
Gross Tank Volume (gals) | 7 | 12 | 20 | 42 | 62 | 87 | 117 | 161 | 245 |
Slurry Capacity (gals) | 2.5-3.5 | 4-6 | 7-9 | 18-20 | 25-28 | 35-39 | 45-50 | 68-75 | 90-100 |
Media Volume (gals) | 3 | 5 | 8 | 18 | 26 | 37 | 47 | 71 | 94 |
HP | 7.5* | 10 | 15 | 20 | 30 | 40 | 50 | 75 | 125 |
Height | 73″ | 86″ | 86″ | 92″ | 98″ | 102″ | 104″ | 118″ | 126″ |
Floor Space (W x D) | 36″x 64″ | 59″x42″ | 59″x42″ | 65″x48″ | 72″x54″ | 78″x55″ | 83″x56″ | 89″x64″ | 94″x72″ |
Machine Weight (lbs) w/o media | 1700 | 2400 | 2700 | 3700 | 4600 | 5000 | 6500 | 8900 | 11,000 |
Equipment can be built to CE specifications, if required.